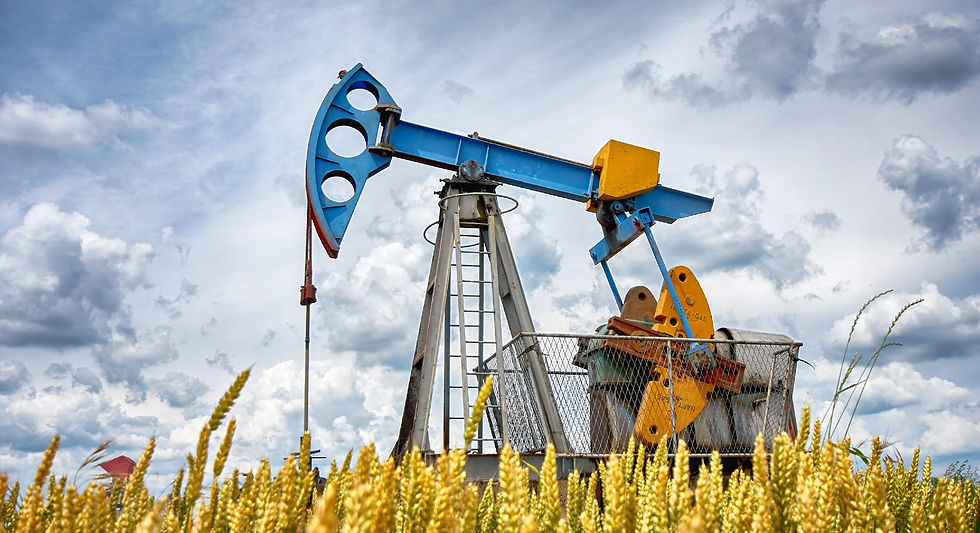
U L T R A C L A D™
PRECISION. PURITY. PERFORMANCE.
BREAKTHROUGH CLADDING TECHNOLOGY
On of the most significant technological breakthroughs to date was the launch of UltraClad™, the world’s first and only fully robotic cladding technology, operating in the continuous 1F welding position, capable of cladding any shape or size pipe. From elbows, bends, tees, laterals, y-laterals, elliptical heads, nipples, crosses or any other type of geometry, the UltraClad™ robotic machines deliver the PURIST, MOST CORROSION & WEAR RESISTANT OVERLAY on the market.
1F welding involves maintaining the welding torch in a downward flat position travelling horizontally while keeping the torch in a vertical position, using gravity to its advantage, allowing the molten metal to draw downward, resulting in a faster and more precise weld. Any other weld position (e.g. 2F or 3F) has to contend with the force of gravity pushing the molten metal downward, which causes the weld to pile up. These methods used by the competition are referred to in the industry as “out of position” welding.
The UltraClad™ proprietary process involves synergic welding with cold metal transfer technology that delivers the coolest interpass temperatures (<900°F), which results in the lowest dilution rates in the industry (<5%). As well, the UltraClad™ technology delivers finished product up to 5x faster and at a significant cost savings advantage.
THE NEW STANDARD

Unique 1" wide weave pattern applied longitudinally, circumferential, spiral or herringbone, all in the 1F position

PRECISION
While the competition welds every pipe as if it were perfectly round, UltraClad™ is the only weld overlay technology in the world that detects any inconsistencies in the pipe’s geometry & ovality (in real-time) and adjusts automatically, ensuring the most accurate and highest quality overlay in the industry.
In addition, UltraClad™ operates within 1mm thickness tolerance and overlay can be applied within 1mm of the flange face.
PURITY
The key to having a pure overlay is found in the ability to achieve the lowest dilution rates possible. While the acceptable industry standard falls between 18% - 20%, UltraClad™ maintains less than 5% dilution. The UltraClad™ proprietary process has the coolest welding temperatures (while maintaining optimal bond), which delivers the lowest dilution rates and results in the most corrosion & wear resistant overlay on the market.
PERFORMANCE
UltraClad™ delivers the purest, the most precise weld overlay on the market, which outlasts and outperforms the competition. UltraClad™ maintains continuous 1F welding no matter how complex the geometry. In addition to having the lowest dilution rates in the industry, UltraClad™ virtually eliminates pipe distortion with less than 1% change in ovality. The UltraClad™ proprietary torches feature a twin-wire configuration, allowing 2-layers of overlay to be deposited with a single pass.

WORLD LEADING TECHNOLOGY
The only automated technology capable of cladding any shape or size pipe, fitting, vessel, heat exchanger, or any other type of geometry, all in the 1F position
HIGHEST QUALITY OVERLAY
Proprietary weld process that never exceeds 900°F and deposits a unique 1" wide layer at a thickness of 1mm - 14mm, with the lowest dilution rate in the industry (less than 5%) and lowest change in ovality (less than 1%)
MOST PRECISE
Thickness tolerance of 1mm and deposit accuracy to 1mm of flange face
FASTEST PRODUCTION TIME
UltraClad™ overlay is applied up to 5 times faster than the competition
MOST COMPETITIVE PRICE
Cost savings up to 30%
MOST ADVANCED METALLURGICAL BOND
Proprietary process ensures a precise bond, allowing for the purest and most uniform overlay
COMPETITIVE ADVANTAGE

The Key is Purity
More than 65% of all pipeline failures are attributed to metal loss. The key to maintaining the longest service life of your components is to minimize metal loss, which is found in the ability to maintain the purity of the weld overlay. And to maintain purity means you need to minimize dilution.
UltraClad™ has the lowest dilution rates in the industry, which means it outlasts and outperforms the competition. Acceptable industry standards of dilution is 18% - 20%. UltraClad™ maintains less than 5% dilution.
According to independent third-party testing, the UltraClad™ overlay actually gets harder as it wears over time. This means the UltraClad™ overlay wears slower and lasts longer.
In addition to having the lowest dilution rates in the industry, UltraClad™ virtually eliminates pipe distortion where the ovality of the pipe is altered by less than 1%.
OVERLAY ALLOYS
JEBCO has the ability to apply a variety of overlay alloys in a single or multiple layer combination, addressing both abrasion and corrosion resistance either individually or in tandem.
Nickel Based Super Alloys
High heat resistant, excellent hardness and strength. Nickel super alloys including: 625, 686, 617, 622, etc.
Chromium Carbide
Extremely hard, corrosion resistant and retains its strength at high temperatures.
Monel 400
High strength and corrosion resistant properties.
Duplex & Super Duplex
Provides high strength/ductility with good corrosion resistance (including stress corrosion cracking).
Stainless Steel
Offers superior resistance to inter-granular corrosion. It’s also suitable for high temperature service, due to its good mechanical properties.
Other Alloys
UltraClad™ is capable of applying various other alloys with the desired properties and optimal specifications.
ULTRACLAD™ APPLICATION HIGHLIGHTS
Superior 1F application
Any shape or size pipe (1.5" and greater)
Purest Overlay (less than 5% dilution)
Capable of applying 1mm to 14mm thickness in a single pass.
Overlay can be applied in any direction (e.g. Longitudinal, Circumferential, Spiral, Herringbone)
Twin torch application is capable of applying two layers of overlay at same time.
Advanced bond between overlay and base metal (meets ASTM A578 requirements)
Meets the requirements of NACE MR0175/ISO 15156 Part 3.
Superior finish (no cracking or defects)
HIGHEST QUALITY STANDARDS
JEBCO recognizes that its customers require the highest quality standards and that’s why in addition to being a certified Controlled Goods Supplier for the Canadian and U.S. Government & Military, JEBCO is accredited to ISO 9001:2015 and proudly holds ASME U certification, enabling us to provide a range of services from full supply of ASME code compliant equipment and pressure vessels to subcontract welding on free-issue ASME standard material.
As well, JEBCO is the only company in the world to receive certification from the Alberta Boilers Safety Association (ABSA) with the unique ability to apply overlay over the pressure boundary of a certified vessel without re-certification.
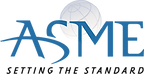


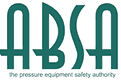

